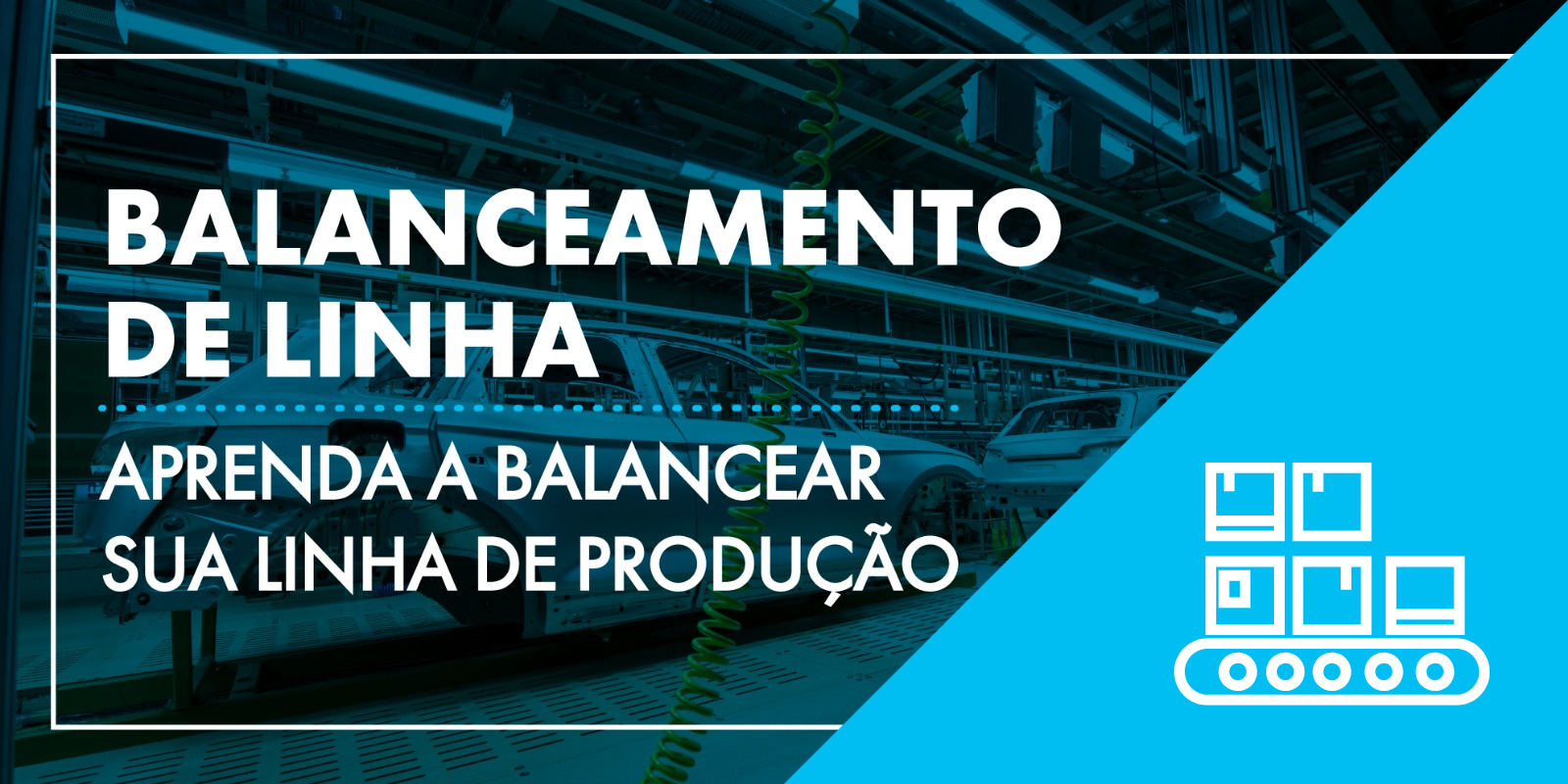
O balanceamento de linha é uma estratégia essencial para aumentar a eficiência industrial e reduzir desperdícios ao longo do processo produtivo. Essa abordagem visa distribuir as tarefas de forma equilibrada entre os postos de trabalho, reduzindo o tempo ocioso e prevenindo a formação de gargalos que possam comprometer a produtividade.
Em um ambiente competitivo, a maximização dos recursos por meio do balanceamento de linha é fundamental para assegurar um fluxo contínuo de produção, adaptado às exigências do mercado.
O presente material tem como objetivo apresentar os princípios do balanceamento de linha, destacando seus benefícios, como o incremento da produtividade, a diminuição dos custos operacionais e a melhoria na utilização dos recursos disponíveis, além de fornecer um roteiro para sua implementação eficiente em processos industriais.
O que é balanceamento de linha?
O balanceamento de linha é uma estratégia utilizada na manufatura para distribuir as atividades de maneira uniforme ao longo do processo produtivo. Seu principal objetivo é manter um fluxo contínuo, evitando gargalos e períodos de ociosidade. Com isso, é possível reduzir sobrecargas em determinadas etapas e eliminar desperdícios, como deslocamentos desnecessários e tempos de espera. Quando aplicado de forma eficiente, esse método aumenta a produtividade, diminui os custos e melhora a capacidade de resposta às demandas do mercado.
Um processo bem estruturado assegura que cada estação de trabalho opere de forma sincronizada, prevenindo acúmulos de materiais e atrasos. Além disso, essa abordagem permite um uso mais eficiente dos recursos disponíveis, contribuindo para a redução dos custos operacionais e o melhor aproveitamento da capacidade instalada.
O balanceamento pode ser realizado manualmente ou com o auxílio de sistemas automatizados. No método tradicional, gestores e operadores fazem ajustes com base na experiência prática e observação direta.
Já a abordagem automatizada utiliza softwares e algoritmos para determinar a distribuição ideal das tarefas, levando em conta fatores como tempo de ciclo, limitações do processo e metas de eficiência. A escolha entre essas alternativas depende da complexidade da operação e do nível de tecnologia adotado pela empresa.
Por que o balanceamento de linha é importante?
Empresas que adotam o balanceamento de linha conseguem aumentar a produção sem precisar de novos investimentos em infraestrutura. Isso ocorre porque a distribuição eficiente das tarefas reduz desperdícios, como tempos ociosos, movimentações desnecessárias e acúmulo de materiais em determinados pontos da linha.
Ao minimizar essas ineficiências, a produção se torna mais fluida, permitindo que os recursos disponíveis sejam melhor aproveitados e resultando em um menor custo por unidade produzida.
A gestão eficiente de insumos, por meio de técnicas como o Kanban no estoque, pode potencializar ainda mais os benefícios do balanceamento de linha, garantindo que os materiais cheguem no momento certo à linha de produção, evitando excessos e faltas que poderiam gerar atrasos ou gargalos.
O impacto na eficiência operacional é significativo, pois um fluxo de trabalho bem estruturado evita gargalos e melhora o desempenho geral da fábrica. Com a produção mais equilibrada, prazos são cumpridos com maior precisão, há uma redução na necessidade de retrabalho e os colaboradores conseguem desempenhar suas funções de maneira mais produtiva. Esse aumento na eficiência torna a indústria mais competitiva, permitindo que ela responda com mais rapidez às demandas do mercado e se diferencie da concorrência.
Indústrias de diferentes segmentos aplicam com sucesso o balanceamento de linha para melhorar seu desempenho. No setor automotivo, por exemplo, montadoras utilizam essa técnica para garantir que cada estação de trabalho opere no mesmo ritmo, evitando atrasos na linha de montagem.
Na indústria de alimentos, o balanceamento ajuda a coordenar a produção para evitar desperdícios e garantir a qualidade do produto final. Já no setor de eletrônicos, fabricantes ajustam suas linhas para otimizar a montagem de componentes e reduzir defeitos. Esses exemplos demonstram como o balanceamento de linha pode ser aplicado em diferentes contextos para maximizar a eficiência e a produtividade.
Principais desafios do balanceamento de linha
Apesar dos benefícios, implementar um balanceamento eficiente pode ser um desafio para muitas empresas, principalmente na identificação de gargalos e restrições de produção. Determinar os pontos críticos onde ocorre o acúmulo de material ou a lentidão do processo exige uma análise detalhada e contínua do fluxo de trabalho. Além disso, pode ser difícil prever com precisão o impacto de certas alterações, o que pode levar a ajustes frequentes para otimizar o balanceamento.
Outro desafio significativo é a resistência dos operadores às mudanças nos processos. Muitas vezes, os colaboradores estão acostumados com uma forma de trabalhar e podem ter dificuldades em adotar novas abordagens ou tecnologias. Superar essa resistência exige uma boa comunicação sobre os benefícios do balanceamento e um suporte adequado para facilitar a transição.
A capacitação e o treinamento da equipe também são fundamentais para o sucesso do balanceamento de linhas. Os operadores e gestores precisam entender a importância da distribuição eficiente de tarefas e como suas ações impactam o desempenho global da produção. Sem o conhecimento adequado, a implementação do balanceamento pode ser comprometida, resultando em resultados abaixo do esperado.
Apesar das vantagens, implementar um balanceamento de linha eficaz pode representar um desafio para muitas empresas, especialmente na identificação de gargalos e restrições ao longo do processo produtivo. Detectar os pontos críticos onde há acúmulo de materiais ou lentidão exige uma análise constante e detalhada do fluxo de trabalho. Além disso, prever com exatidão os impactos de determinadas mudanças nem sempre é simples, o que pode levar à necessidade de ajustes frequentes para manter a eficiência.
Um fator que pode contribuir positivamente para esse equilíbrio é o bom endereçamento de estoque. Quando os materiais estão organizados de forma estratégica e acessível, há uma redução significativa no tempo gasto com movimentações desnecessárias, o que evita atrasos entre as etapas de produção. Uma gestão eficiente do estoque, com localização adequada dos insumos, favorece a fluidez das operações e facilita o abastecimento das estações de trabalho, colaborando diretamente com o balanceamento da linha.
Outro desafio comum é a resistência dos operadores frente às mudanças nos processos. Muitas vezes, os colaboradores estão habituados a uma determinada rotina e podem encontrar dificuldades ao adotar novos métodos ou tecnologias. Superar essa barreira exige uma comunicação clara sobre os benefícios das mudanças, além de suporte constante para garantir uma transição tranquila.
Por fim, a capacitação da equipe é essencial para o sucesso do balanceamento de linha. Gestores e operadores precisam compreender a importância da distribuição equilibrada de tarefas e como suas atividades impactam a performance do processo como um todo. Sem conhecimento adequado, a implementação corre o risco de não atingir os resultados esperados, comprometendo o desempenho produtivo da organização.
Como fazer um balanceamento de linha eficiente?
Para garantir um balanceamento de linha eficiente, é fundamental seguir um processo estruturado que permita uma análise precisa da produção. O primeiro passo é mapear todas as etapas do processo produtivo, identificando as atividades realizadas, seus respectivos tempos de execução e os responsáveis por cada tarefa.
A partir dessa análise, é possível redistribuir as tarefas entre os postos de trabalho, de forma que a carga de atividades seja equilibrada. Isso evita acúmulos em determinadas estações e reduz o tempo de espera entre as etapas, melhorando o fluxo geral da produção.
A padronização dos tempos de operação é outro fator essencial nesse processo. Quando cada tarefa possui um tempo bem definido e replicável, é possível manter um ritmo constante ao longo da linha, facilitando o controle da produção e reduzindo variações indesejadas.
Essa padronização também permite maior previsibilidade, o que ajuda no planejamento de recursos e na tomada de decisões. Além disso, garante que todos os operadores sigam os mesmos procedimentos, aumentando a consistência e a qualidade do produto final.
Por fim, é importante adotar métodos que permitam ajustar a carga de trabalho entre operadores e máquinas. Isso pode incluir a reorganização das tarefas com base na capacidade individual de cada estação, o uso de equipamentos para automatizar processos repetitivos ou o revezamento de funções para reduzir a fadiga.
Esses ajustes devem considerar tanto a eficiência operacional quanto o bem-estar dos colaboradores. Ao alinhar corretamente o esforço humano e o uso da tecnologia, é possível alcançar um desempenho mais uniforme e produtivo em toda a linha.
Ferramentas para otimizar o balanceamento de linha
Diversas ferramentas podem ser aplicadas para analisar e otimizar o balanceamento de linha, sendo uma das mais eficientes o Diagrama de Yamazumi.
Essa ferramenta visual organiza as tarefas em barras verticais, representando o tempo necessário de execução em cada posto de trabalho. Com ela, é possível visualizar claramente os desequilíbrios, como estações sobrecarregadas ou com tempo ocioso, facilitando os ajustes necessários para distribuir melhor as atividades.
O uso do Diagrama de Yamazumi é especialmente útil no contexto do balanceamento de linhas de montagem, onde a divisão equilibrada de tarefas entre os postos é essencial para manter a fluidez e a produtividade da operação. A análise de gargalos também se destaca como uma ferramenta estratégica no balanceamento de linha, ajudando a identificar os pontos do processo que estão atrasando o ritmo da produção.
Essa avaliação pode ser feita por meio de observações diretas no chão de fábrica, coleta de dados ou softwares específicos. O balanceamento de linhas de montagem, onde cada estação depende da anterior, um gargalo pode comprometer toda a eficiência do sistema.
Por isso, ao detectar essas restrições, é possível redistribuir tarefas, aumentar os recursos disponíveis em determinados pontos ou até investir em melhorias tecnológicas para eliminar os entraves e garantir um fluxo contínuo.
Além das ferramentas visuais e da análise direta, o uso de softwares especializados tem ganhado destaque no balanceamento de linha. Programas de simulação e modelagem, como o Arena Simulation ou o FlexSim, permitem testar diferentes configurações e cenários antes de realizar alterações reais na produção.
Em linhas de montagem mais complexas, esses sistemas se tornam grandes aliados, pois oferecem uma visão detalhada das interações entre operadores, máquinas e tarefas. Com isso, é possível realizar ajustes mais precisos, reduzir desperdícios e alcançar um nível de balanceamento mais eficiente e sustentável.
Exemplo de otimização de processos produtivos
A EPR possui ampla experiência na condução de projetos voltados à otimização de processos produtivos, com foco na identificação e eliminação de gargalos, melhoria do fluxo operacional e aumento da produtividade.
Entre os casos de destaque está o projeto realizado junto a uma importante indústria de embalagens do Rio Grande do Sul. O trabalho teve como foco o balanceamento de linha em um dos setores da empresa, onde foram identificadas ineficiências significativas relacionadas aos tempos de setup das máquinas e à distribuição das tarefas entre os operadores.v
Durante o projeto, a equipe da EPR realizou um mapeamento completo das etapas envolvidas na preparação das máquinas, o que possibilitou a identificação precisa dos gargalos existentes. Foi constatada uma concentração de tarefas críticas em determinados momentos da operação, o que causava acúmulo de atividades e ociosidade em outras fases. Através da análise dos tempos de cada subprocesso, foi possível redistribuir as atividades de forma mais equilibrada ao longo do fluxo produtivo.
Essa nova distribuição permitiu um melhor aproveitamento dos recursos disponíveis, reduzindo tempos ociosos e aumentando a eficiência das linhas. O balanceamento de linha contribuiu diretamente para a redução do tempo total de setup, refletindo em um maior tempo efetivo de produção. Além disso, a padronização das etapas e a reorganização das funções contribuíram para uma operação mais fluida e com menos retrabalho.
Como resultado, a indústria alcançou um aumento significativo na produtividade do setor, acompanhado por maior previsibilidade operacional e redução de custos associados a paradas não planejadas e desperdícios.
O projeto demonstrou, de forma concreta, o impacto positivo que o balanceamento de linha, aliado a uma análise técnica minuciosa dos processos, pode gerar na eficiência e na dinâmica produtiva. Este caso reforça o compromisso da EPR com a entrega de soluções sob medida, orientadas por resultados e com elevado valor agregado para seus clientes.
Conclusão
Para otimizar a eficiência produtiva e minimizar desperdícios, o balanceamento de linha deve ser implementado de forma estratégica, considerando as particularidades do processo produtivo e os recursos disponíveis.
A adoção de técnicas estruturadas permite distribuir as tarefas de maneira equilibrada, garantindo um fluxo contínuo e reduzindo tempos ociosos e sobrecargas em determinados postos de trabalho.
Ferramentas como o Diagrama de Yamazumi são essenciais para visualizar a alocação das atividades e identificar possíveis desequilíbrios na linha de produção. Além disso, a Análise de Gargalos possibilita a detecção de restrições que limitam o desempenho do sistema produtivo, permitindo ajustes que otimizam o fluxo de trabalho e aumentam a eficiência operacional.
Ao incorporar essas práticas ao planejamento da produção, sua empresa poderá aumentar a produtividade, reduzir custos operacionais e melhorar a utilização dos recursos disponíveis. Com um processo mais equilibrado e eficiente, a organização se torna mais competitiva, fortalece sua posição no mercado e garante maior sustentabilidade no longo prazo.
Baixe agora nossa Planilha de Gestão de Estoques e descubra como otimizar ainda mais sua linha de produção!