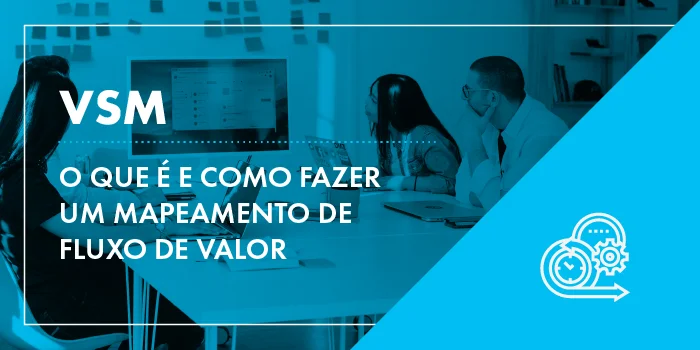
VSM (Value Stream Mapping) ou MFV (Mapeamento de Fluxo de Valor) são as siglas que denotam uma ferramenta desenvolvida para analisar e melhorar o passo a passo para entregar um determinado produto ou serviço. Vale comentar a importância desse recurso para qualquer empresa, pois torna a compreensão dos processos bem mais visual.
Esse fluxograma, que acompanha do início ao fim um processo, utiliza um sistema de símbolos próprios para representar as atividades. Além disso, um fluxo de informações bem estabelecido torna-se extremamente útil para monitorar e estimar o lead time de produção. Por isso neste artigo, você vai ver os benefícios de utilizar o Mapeamento de Fluxo de Valor e de que forma ele pode ser construído.
O que é VSM, ou Mapeamento de Fluxo de Valor?
O VSM é um diagrama que mostra todas as etapas necessárias para a entrega de um produto ou serviço, incluindo o fluxo de materiais e informações. Em geral, faz-se um mapa do estado atual e outro do estado futuro, evidenciando as oportunidades de melhorias e otimizações possíveis.
Dessa forma, ao distribuir os tempos de cada etapa necessária e calcular o lead time de estoques intermediários, visualiza-se de forma macro toda a produção. A partir disso, por meio da estratégia, é possível classificar os processos de três maneiras:
- Processos que agregam valor
- Processos que não agregam valor, porém são relevantes para a qualidade
- Processos que não agregam valor e não são relevantes
Com essas classificações, é possível eliminar ou diminuir essas etapas que não agregam valor ao produto ou serviço prestado.
Qual a relação entre VSM e Lean Seis Sigma?
O VSM é uma ferramenta que foi criada a partir da metodologia do Lean Manufacturing, que busca a maximização da redução de desperdícios. No início da década de 1950, a Toyota iniciou a implantação dos métodos de MFV, mudando a indústria de manufatura.
O Seis Sigma busca por redução de variabilidade e aumento da estabilidade dos processos e, junto ao Lean, impulsiona os objetivos de maior padronização de otimização do fluxo produtivo em qualquer empresa. Para isso, o VSM é fundamental, pois proporciona a visualização da movimentação de informações e materiais de forma clara e detalhada.
A redução de tempos de setup, eliminação de estoques intermediário e o redesenho dos processos de maneira mais eficiente são apenas algumas das melhorias que a aplicação do MFV pode promover. Para isso, esse recurso não é um resultado em si, mas sim um meio de analisar o que pode ser mudado, tornando a entrega final mais adequada para o cliente.
Quais são os benefícios do VSM?
Uma companhia que faz uso do Mapeamento de Fluxo de Valor consegue ter uma visão macro de seus processos, analisando sistemicamente as atividades, os tempos e os transportes. Portanto, é possível ver de forma mais clara os pontos de melhoria que trarão mais valor ao cliente e eliminar desperdícios que encarecem ou atrasam a entrega do produto final.
Ainda podemos listar mais alguns pontos nos quais o VSM pode ajudar uma empresa:
1. Promove a execução decisiva de melhorias
Com o MFV em mãos, a visualização do que pode ser melhorado em um estado futuro se torna mais fácil. Portanto, a decisão de comprar mais máquinas, por exemplo, pode acontecer com embasamento e de acordo com a estratégia de cada organização.
2. Ajuda na estruturação de um sistema de indicadores de desempenho (KPIs)
Como disse William Edwards Deming – professor, universitário, autor, palestrante e consultor estadunidense -, “O que não pode ser medido, não pode ser gerenciado”. Assim, ter indicadores válidos e confiáveis para avaliar o progresso de qualquer companhia é essencial para a sua evolução. O acompanhamento desses números é fundamental para melhor gestão do negócio.
3. Facilita a classificação dos processos dentro de uma organização
O estabelecimento de início e fim de cada processo, por exemplo, facilita a compreensão de qual ou quais necessitam maior otimização. A partir disso, a tomada de decisão dos gestores quanto a quem cobrar ou ao que precisa de mais atenção se torna muito mais correta.
Quais desperdícios o VSM evita?
Utilizar o Mapeamento de Fluxo de Valor na sua companhia poderá ajudá-lo a reduzir ou até eliminar as Sete Perdas da Produção de acordo com o Lean Manufacturing, sendo elas:
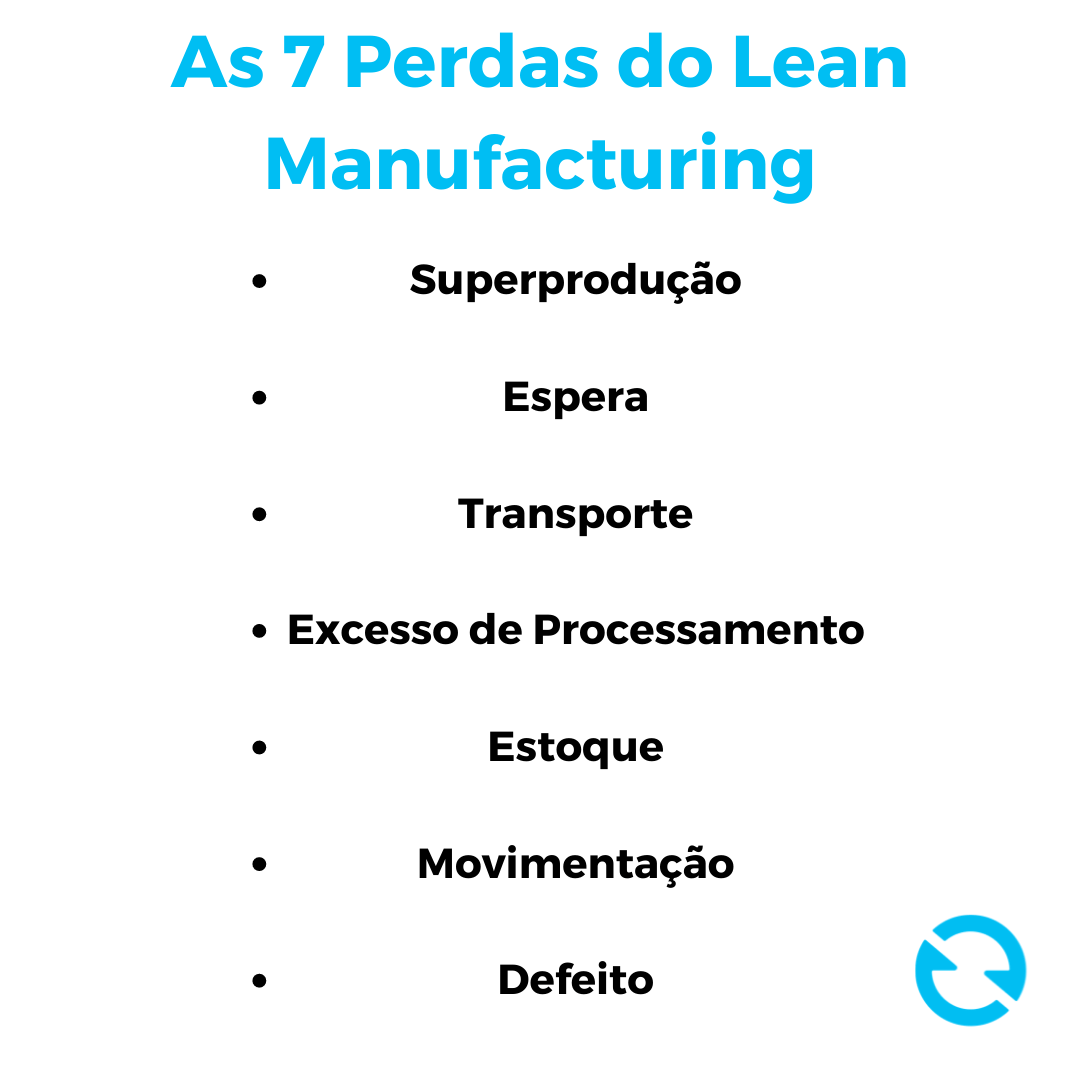
1. Perda por Superprodução
Quando a quantidade produzida é maior do que a necessária. Além de poder acontecer por mal planejamento, deve se considerar a possibilidade do desbalanceamento das linhas produtivas, gerando altos estoques, por exemplo.
2. Perda por Espera
Tem causa no excesso de tempo entre uma etapa e outra da produção, levando a um lead time mais alto do que o necessário. Dessa maneira, acarreta em mais estoques intermediários, podendo afetar até mesmo o espaço físico para trabalho.
3. Perda por Transporte
Quando se transporta um produto de maneira exagerada ou desnecessária, em geral devido a uma logística e a um layout não otimizados. AssIm, com maior proximidade entre os setores produtivos, esse tempo desperdiçado em transporte poderia ser investido em mais produção.
4. Perda por Excesso de Processamento
Ocorre quando o processo de produção contém etapas a mais do que necessário. Portanto, pode-se eliminar tais etapas “extras” sem que ocorra comprometimento do produto. Por meio da distribuição dos tempos de cada etapa, o MFV permite a análise mais assertiva quanto a processamentos desnecessários.
5. Perda por Estoque
Quando há excesso de estoque de materiais e produtos acabados, gerando gastos desnecessários com insumos, produção e espaço físico. Nesse sentido. em geral ocorre pelo erro de cálculo de insumos e superprodução.
6. Perda por Excesso de Processamento
São as movimentações desnecessárias dos colaboradores nos processos de produção. Dessa forma, as causas mais comuns são erros de orientação na execução, má distribuição de tarefas, falta de parâmetros quanto a tempo para executar cada atividade e também layouts mal organizados.
7. Perda por Defeito
Ocorre se o produto está fora dos padrões de qualidade necessários. Gera o desperdício de recursos financeiros, além da possibilidade de custo extra para conserto. Dessa forma, a falta de acompanhamento das não-conformidades, por meio de indicadores, gera cada vez mais custos às empresas.
Além das Sete Perdas, será possível enxergar quais tipos de processos agregam ou não valor e se eles devem ou não seguirem por motivo de qualidade ao serviço ou produto final.
Como fazer um VSM passo a passo?
Para desenhar um VSM, há algumas etapas para garantir o sucesso no uso dessa ferramenta. Nesse sentido, é importante lembrar que para a realização do Mapeamento de Fluxo de Valor é essencial a participação de um grande número de pessoas, em especial do setor que se deseja avaliar.
As etapas cruciais para o mapeamento são:
- Estabelecer os responsáveis
Definir as pessoas de diferentes níveis (estratégico, gerencial e operacional) e departamentos que irão fazer o desenho do processo total.
- Identificar a família de produtos
É preciso agrupar e identificar as famílias de produtos que serão mapeadas em um determinado fluxo de valor. Aglomeram-se tais famílias de acordo com os processos de produção pelo qual passam.
- Desenhar o processo atual
Fazer o mapeamento de fluxo de valor atual da companhia é fundamental para averiguar a situação da empresa como um todo. Portanto, deve ser analisado o estoque geral, a quantidade de trabalhadores, os turnos de funcionamento, o tempo de ciclo das atividades, as taxas de desperdício e os índices de defeitos.
- Definir o estado futuro e criar planos de ação
A partir do VSM atual e da análise dos desperdícios, concluindo-se o que pode ser eliminado, a companhia pode se planejar e definir o que pode ser feito para melhorar os processos. Assim, o lead time de produção torna-se cada vez menor, indicando possibilidade para aumento de produtividade.
Exemplo de VSM
Abaixo temos um exemplo de mapeamento de fluxo de valor, no qual podemos perceber os seus principais símbolos e regras. Nesse sentido, o cliente deve ficar sempre à direita do mapeamento, e o fornecedor à esquerda.
Nota-se também que o Planejamento e Controle da Produção (PCP) fica ao centro, e saem dele setas que se comunicam com cada processo ou setor da empresa. Além disso, é interessante ressaltar que em sistemas empurrados de produção existem várias setas entre o PCP e os setores. Enquanto isso, em sistemas puxados apenas uma seta sai do PCP para se comunicar com um único processo, geralmente um dos últimos da ordem produtiva.
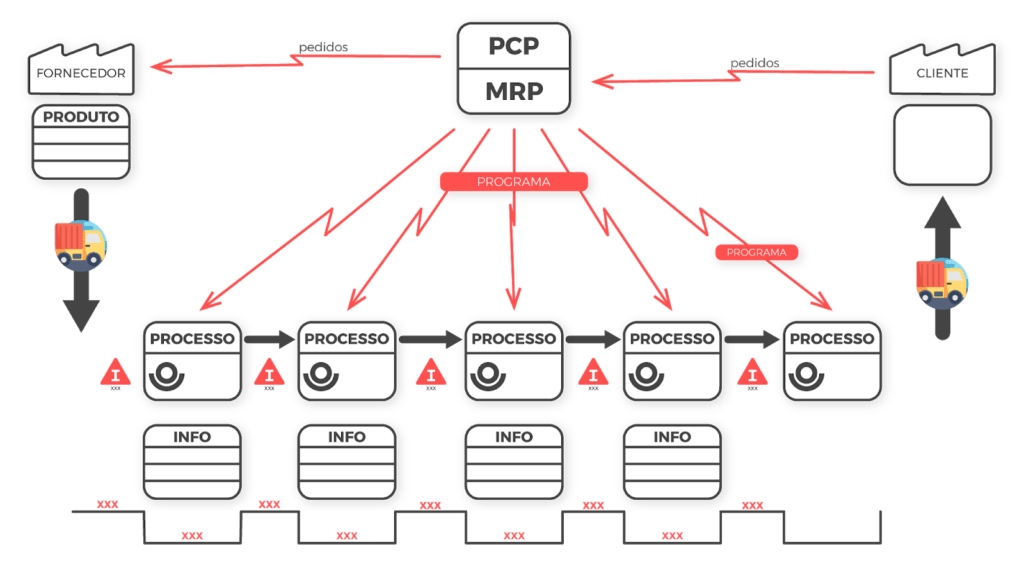
Os ícones utilizados estão demonstrados na figura abaixo, e é possível perceber que existem opções para montar o mapeamento de qualquer tipo de negócio.
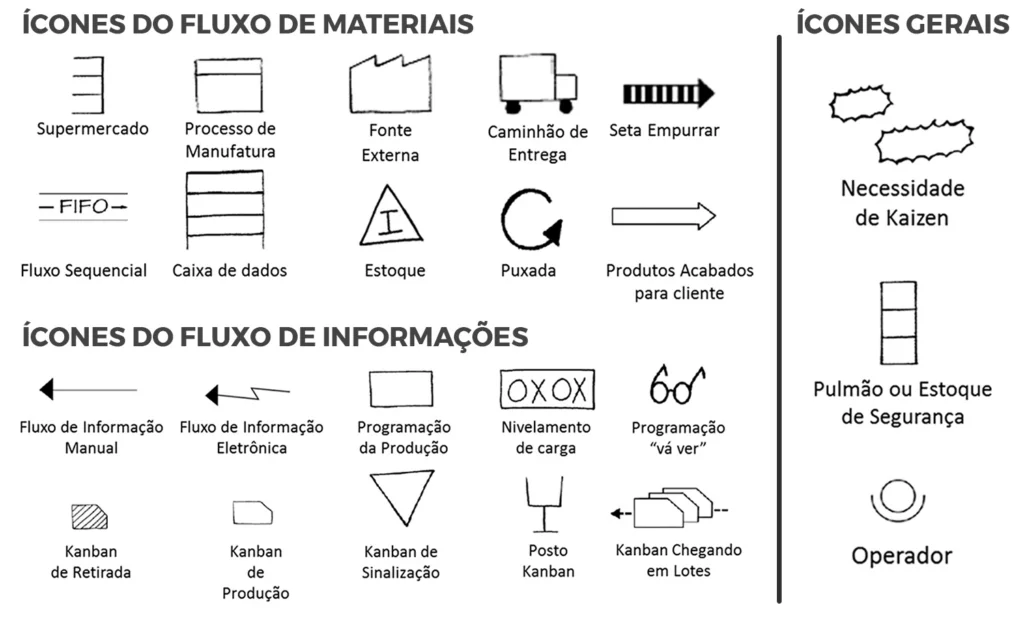
Com o MFV, pode-se entender todo o fluxo produtivo, pois a variedade de simbologia e informações torna o mapa muito completo e detalhado. Portanto, percebe-se a importância que essa ferramenta pode ter para auxiliar os gestores de uma empresa a tomarem decisões melhores quanto ao funcionamento da fábrica, por exemplo.