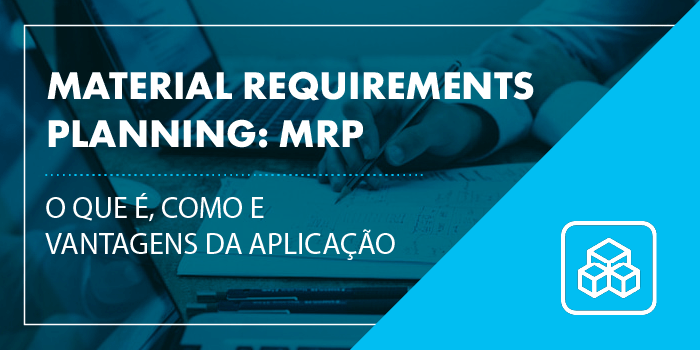
O Manufacturing Resource Planning ou Material Requirements Planning (MRP) traduz-se como o planejamento de recursos da manufatura. Dessa forma, é uma ferramenta que realiza cálculos com o intuito de compreender o melhor momento para comprar os materiais necessários à produção.
Portanto, a sua implementação na empresa pode ocasionar diversos benefícios como redução de custos, eficiência na gestão do estoque e movimentação otimizada dos materiais na fábrica.
Nesse contexto, ressalta-se que para o funcionamento do sistema MRP é necessário que a empresa disponibilize dados como demanda, lista de materiais e saldo de estoque. A partir dessa listagem, o MRP executa os cálculos com a finalidade de diminuir a possibilidade de escassez ou excesso de material e auxilia nas tomadas de decisão.
O que é MRP?
O MRP é uma metodologia que ajuda no planejamento de todas as fases onde os materiais participam do ciclo produtivo, desde o posicionamento na linha de produção até seu armazenamento.
Essa metodologia surgiu na década de 60, época em que os avanços tecnológicos já permitiam o acesso a dados importantes para a implementação do sistema. Entretanto, o conceito atual do método não é o mesmo que em 1960 pois, ao longo do tempo, aconteceram evoluções e modificações até chegar-se ao contexto atual.
Quais são os benefícios do MRP?
Os benefícios da implementação do sistema são diversos, englobando, assim, todas as áreas de uma empresa. Logo, essa metodologia pode auxiliar tanto a nível micro quanto a nível macro.
Nesse sentido, é importante frisar que a metodologia possibilita um planejamento empresarial mais eficiente visto que as ações desta são mais rápidas e assertivas devido às informações concisas na base de dados.
Dessa forma, a otimização de recursos pela companhia gera benefícios na redução dos níveis de atrasos, na redução dos níveis dos estoques e na redução das falhas humanas.
Quando implementar o Sistema MRP?
O sistema torna-se fundamental naquelas empresas em que existe, na sua linha de produção, processos complexos. Diante disso, quando ocorrem problemas no controle de componentes e mudanças constantes no fluxo de fabricação, se torna imprescindível a implementação do sistema.
De forma geral, é importante manter a harmonia entre as partes envolvidas no processo produtivo, como materiais, mão de obra e fornecedores. Caso contrário, haverá atrasos constantes nos prazos de entrega e níveis elevados de estoques, configurando, assim, mais sinalizadores para a urgência de implementar a metodologia.
Como funciona o sistema MRP?
O funcionamento do sistema tem como base três pilares: saldo de estoques, lista de materiais e demanda. Com essas informações reunidas, o sistema indica a quantidade e quando deve ocorrer a compra de matérias-primas, além de definir o ritmo da produção. Dessa forma, há uma redução na possibilidade de se gargalos produtivos.
Ademais, a automatização do processo auxilia a empresa no cenário competitivo do mercado atual. Como o sistema mecaniza tudo, erros são diminuídos e atrasos nas entregas são evitados. Logo, os pedidos serão entregues aos clientes no tempo exato, aumentando a qualidade de suas entregas.
Quais são os parâmetros fundamentais do MRP?
Nesse contexto, alguns parâmetros são fundamentais para o funcionamento eficiente da metodologia.
- Tempo de reposição e fabricação
- Dimensão de estoque
- Definição do lote de reposição e fabricação
Todos esses fatores credibilizam o sitema a ser uma metodologia adequada para aprimorar o processo de planejamento dos materiais de uma empresa. Dessa forma, haverá uma confiabilidade neste processo, o que acarreta em erros humanos reduzidos e estoques melhor geridos.
O que é MRP 1 e 2?
O MRP I é o Material Requirements Planning, ou seja, Planejamento das Necessidades de Material. Sendo assim, ele calcula a produção necessária, mas não considera a capacidade da fábrica. Portanto, nessa metodologia é importante o apoio dos gerentes responsáveis na disponibilização dos dados referentes à demanda.
Por outro lado, o MRP II é o Manufacturing Resource Planning, ou seja, Planejamento dos Recursos de Produção. Além de englobar o MRP I, o MRP II considera a capacidade fazendo com que se tenha um planejamento mais eficaz de acordo com as informações dadas.
Características do MRP 1
O MRP I envolve características diversas dentro de uma indústria, contudo, não englobam questões relacionadas à capacidade produtiva. Algumas das principais características são:
- Gestão de pedidos
- Solicitações de compra
- Plano de produção
- Políticas de estoque
- Cadastro de matérias-primas
Todos esses elementos do MRP I contribuem de forma significativa para o planejamento dos recursos para uma empresa, mas, deixam uma lacuna na capacidade. Por isso, na medida em que houve os avanços tecnológicos, o MRP I também se apropriou de inovações para melhorar o sistema.
Características do MRP 2
O MRP II assume todos os elementos vinculados ao MRP I, além de considerar a capacidade atual e estratégias pertencentes à demanda. Dessa forma, o MRP II é um sistema mais robusto e consistente, permitindo que o foco não seja apenas as operações, mas também o empreendimento como um todo.
Sua principais características são:
- Tabela dos recursos disponíveis
- Roteirização e lead time da produção
- Calendário de disponibilidade dos insumos
A partir de diversas características, ocorre o auxílio na execução do sistema MRP e, consequentemente, no planejamento eficiente das fases do ciclo de produção.
Como calcular o MRP?
O cálculo do MRP segue uma lógica de determinar as datas em que as etapas são iniciadas e concluídas. O cálculo ocorre por meio de um passo a passo:

Podemos iniciar pela definição do plano de produção, que permite a visualização do panorama geral da empresa, identificando o que deve ser produzido.
Na sequência, o próximo passo tem como finalidade a identificação da necessidade dos materiais. Para isso, o MRP faz a separação dos itens de uma estrutura com o intuito de facilitar o cálculo para saber a quantidade ideal de cada material.
Por último, ocorre o desenvolvimento do cálculo para saber as quantidades ideais. Todo esse sequenciamento apresentado é realizado de forma automatizada pelo sistema, assim, pode-se perceber a sua importância.
Diferenças entre MRP e ERP
O Enterprise Resource Planning (ERP) tem como tradução Planejamento de Recursos Empresariais. Esse sistema busca a integração dos departamentos de uma empresa por meio de sistema computacional, que possibilita o gerenciamento e a centralização das informações. Dessa forma, sendo um sistema mais completo que o MRP.
A principal diferença entre os sistemas é que o MRP é uma ferramenta que funciona de maneira independente, enquanto o ERP precisa englobar os dados de diversas áreas. Por fim, vale ressaltar que o ERP engloba tanto o MRP I como o MRP II.