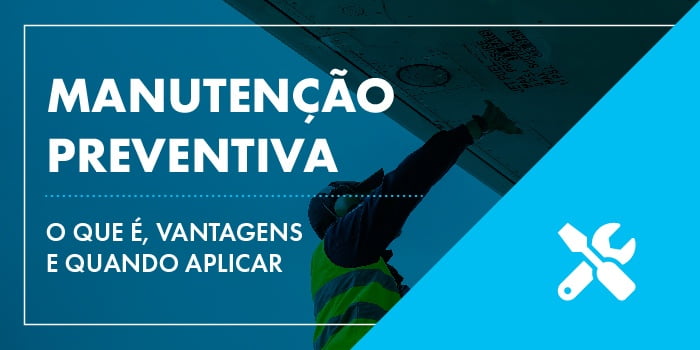
A manutenção preventiva é a manutenção realizada de maneira planejada e em intervalos predeterminados. Sendo assim, é muito importante para garantir a eficiência dos equipamentos em operação, garantindo a qualidade dos produtos.
Nesse contexto, ter conhecimento sobre manutenção preventiva é necessário para evitar prejuízos no seu negócio. Portanto, por meio desse texto, você compreenderá as vantagens e desvantagens da manutenção preventiva, quando e como implementá-la, além de saber diferenciá-la da manutenção corretiva e da manutenção preditiva.
O que é manutenção preventiva?
A manutenção preventiva é um conjunto de atividades de revisão, controle e monitoramento dos equipamentos realizada de maneira planejada e em intervalos predeterminados. Portanto, todas as etapas desse tipo de manutenção são definidas com antecedência, de forma que a intervenção ocorre antes do surgimento de uma falha.
Esse tipo de manutenção fundamenta-se em alguns critérios, também chamados de “gatilhos”, os quais dependem do maquinário e do tipo de produção adotado pela empresa. Dessa forma, quando esses parâmetros são definidos, a manutenção deve ser realizada. São eles:
- Tempo: intervalos predeterminados, definidos pela empresa ou recomendados pelo fabricante do equipamento. Por exemplo, realizar calibragem a cada 6 meses.
- Horas de funcionamento: quanto tempo o equipamento pode estar em operação. Por exemplo, realizar a lubrificação de uma máquina a cada 200 horas de operação.
- Produtividade: quantidade de itens produzidos. Por exemplo, realizar a substituição da serra de uma máquina de corte a cada 1500 peças produzidas.
- Misto: é a junção dos gatilhos citados anteriormente, o que ocorrer primeiro acarreta a manutenção.
Qual a diferença entre manutenção preventiva e preditiva?
Uma situação comum é a confusão entre manutenção preventiva e preditiva. A manutenção preventiva não leva em consideração o real estado de funcionamento do equipamento. Ou seja, ela ocorre de forma programada com base em um cronograma e em informações mais genéricas, tal qual a recomendação do fabricante.
Por sua vez, a manutenção preditiva é capaz de fazer o diagnóstico preciso de quando um componente irá falhar. Dessa forma, é possível obter um melhor aproveitamento da vida útil do elemento, antes da manutenção ser realizada.
Portanto, a manutenção preventiva é bastante recomendada quando o risco de falhas pode gerar alto impacto negativo. Por exemplo, para evitar ou adiar surpresas quanto ao funcionamento do motor de um carro, a troca de óleo do motor deve ser periódica, para mantê-lo lubrificado.
Enquanto isso, a manutenção preditiva busca encontrar o momento ideal para realizar o devido ajuste, evitando custos desnecessários. Logo, o acompanhamento quanto ao funcionamento de uma máquina, por exemplo, frequentemente acontece. Porém nem sempre com necessidade de intervenções, evitando parada de produção e investimentos significativos em manutenções preventivas e/ou corretivas.
E qual a diferença entre manutenção preventiva e corretiva?
Conforme mencionado anteriormente, a manutenção preventiva busca evitar a ocorrência de falhas no equipamento. Em contrapartida, a manutenção corretiva é realizada quando a quebra da peça ou a queda de eficiência já ocorreu, havendo necessidade de correção imediata. É importante ressaltar que a manutenção corretiva não possui necessariamente caráter inesperado, já que pode-se optar por realizar o reparo após a ocorrência da falha, com o auxílio de previsões.
A falta de regularidade para acompanhamento de indicadores quanto ao funcionamento de uma peça, por exemplo, pode indicar custos altos e desperdícios desnecessários para uma empresa. O impacto que a manutenção corretiva pode ter para a produção de uma fábrica pode ser enorme. Considerando que apenas a única ponte-rolante para movimentar vergalhões de aço em uma indústria siderúrgica estraga, além do custo altíssimo para consertá-la, toda a produção para pela dependência da máquina danificada.
Por isso, a manutenção preventiva e/ou preditiva são importantes para evitar impactos que desestabilizem a produção de uma fábrica, por exemplo. Além disso, também se tornam fundamentais para evitar ou adiar falhas que podem atingir a saúde de um operador.
Qual é o objetivo da manutenção preventiva?
Com o passar do tempo, a performance do equipamento decai. Nesse cenário, a manutenção preventiva tem o objetivo de reduzir a probabilidade de falha ou degradação do equipamento ao atuar antes da ocorrência do problema. Dessa forma, a vida útil do dispositivo é preservada e as paradas repentinas na cadeia produtiva são evitadas.
Além disso, sabe-se que equipamentos desgastados prejudicam a qualidade e a velocidade da produção. Portanto, a manutenção preventiva é relevante para evitar não só a baixa eficiência dos equipamentos em operação, como também permite manter a capacidade produtiva de uma fábrica de carros, por exemplo.
Porém, existem estratégias mais avançadas que oferecem uma gestão de ativos mais eficaz e adaptada às necessidades específicas de cada operação. A Manutenção Baseada na Condição (MBC), também conhecida como Preditiva, utiliza tecnologias, como sensores e análise de dados, com o objetivo de monitorar as condições operacionais dos equipamentos. Dessa forma é possível realizar manutenções apenas quando sinais de falha são detectados, evitando intervenções desnecessárias.
Outra opção é a Manutenção de Oportunidade, que foca em aproveitar momentos de parada planejada para realizar manutenções adicionais. Além disso, a Manutenção Centrada na Confiabilidade (RCM) avalia o risco de falhas de cada máquina, permitindo a definição de planos de manutenção customizados.
Quer saber mais sobre qualidade? Clique aqui!
Quais são as falhas evitadas pela manutenção preventiva?
A manutenção preventiva evita falhas relacionadas ao envelhecimento e desgaste do equipamento, as quais possuem prazo variado de incidência. Em geral, elas aparecem em dois grupos:
Falha Potencial
Esse tipo de falha se refere a quando o equipamento apresenta algum defeito, mas ainda assim consegue desempenhar a sua função. Apesar de o problema estar em estágio inicial, se não solucionado, a eficiência do equipamento vai diminuindo ao longo do tempo, culminando em uma falha funcional.
Falha Funcional
A falha funcional é um estágio mais avançado da falha potencial e faz com que o equipamento seja impossibilitado de desempenhar a sua função. Dessa forma, o equipamento enquadra-se no estado de operação abaixo do nível definido como satisfatório ou de completa perda de função.
Nesse contexto, a manutenção preventiva é feita antes ou imediatamente depois da falha potencial ocorrer. Isso evita com que o equipamento chegue no estágio de falha funcional. Além disso, quanto mais próximo do estágio inicial da falha potencial a manutenção for feita, menor é o custo por falta de aproveitamento da vida útil da peça.
O uso de cartas de controle pode ser integrado à manutenção preventiva para monitorar e controlar a variabilidade dos processos produtivos, garantindo que as máquinas operem dentro dos padrões desejados. Leia mais sobre isso no nosso conteúdo!
Quais são as vantagens e desvantagens da manutenção preventiva?
A manutenção preventiva possui vantagens e desvantagens, as quais devem ser levadas em consideração para implementá-la na sua empresa.
Vantagens:
- Aumento da vida útil dos equipamentos pela redução a exposição a falhas e desgastes;
- Redução de acidentes, já que equipamentos operando corretamente promovem maior segurança no trabalho;
- Tempo disponível para a montagem de orçamento pela análise da relação custo-benefício dos materiais a serem comprados;
- Garantir a qualidade dos produtos e a capacidade produtiva;
- Maior agilidade na resolução de problemas, pois com a revisão periódica pode-se detectar falhas em sua fase inicial;
- As paradas na produção para manutenção, por serem planejadas, podem ser efetuadas em um momento que minimize as perdas.
Desvantagens:
- Requer trabalho constante de manutenção e registro das intervenções feitas;
- Possibilidade de introdução de erros na hora de realizar a manutenção;
- Pode acarretar gastos desnecessários a partir da manutenção de peças boas, que demorariam a apresentar falhas.
Além disso, a implementação da manutenção preditiva enfrenta desafios, especialmente na gestão eficaz de dados. Como essa abordagem depende de sensores para realizar um monitoramento contínuo, gera-se uma grande quantidade de dados em tempo real. Por fim, a análise desses dados requer ferramentas avançadas de inteligência artificial e treinamento especializado, o que pode ser um obstáculo para empresas em início de implementação.
Quando devo fazer um plano de manutenção preventiva?
A manutenção preventiva deve acontecer quando equipamentos possuem falhas relacionadas ao tempo e ao uso, em que há um padrão para a ocorrência de defeitos. Assim, é possível seguir um planejamento e manter a periodicidade, com base em análises estatísticas sobre o funcionamento esperado do equipamento e a recomendação dada pelo fabricante.
Além disso, pela relação custo-benefício, recomenda-se que a manutenção preventiva seja aplicada em equipamentos de prioridade média para o fluxo produtivo. Quando esse tipo de equipamento falha, geram prejuízos, mas há baixo risco de acidentes e podem ser consertados rapidamente. Confira abaixo um diagrama comparativo em relação a quando se recomenda utilizar cada tipo de manutenção:
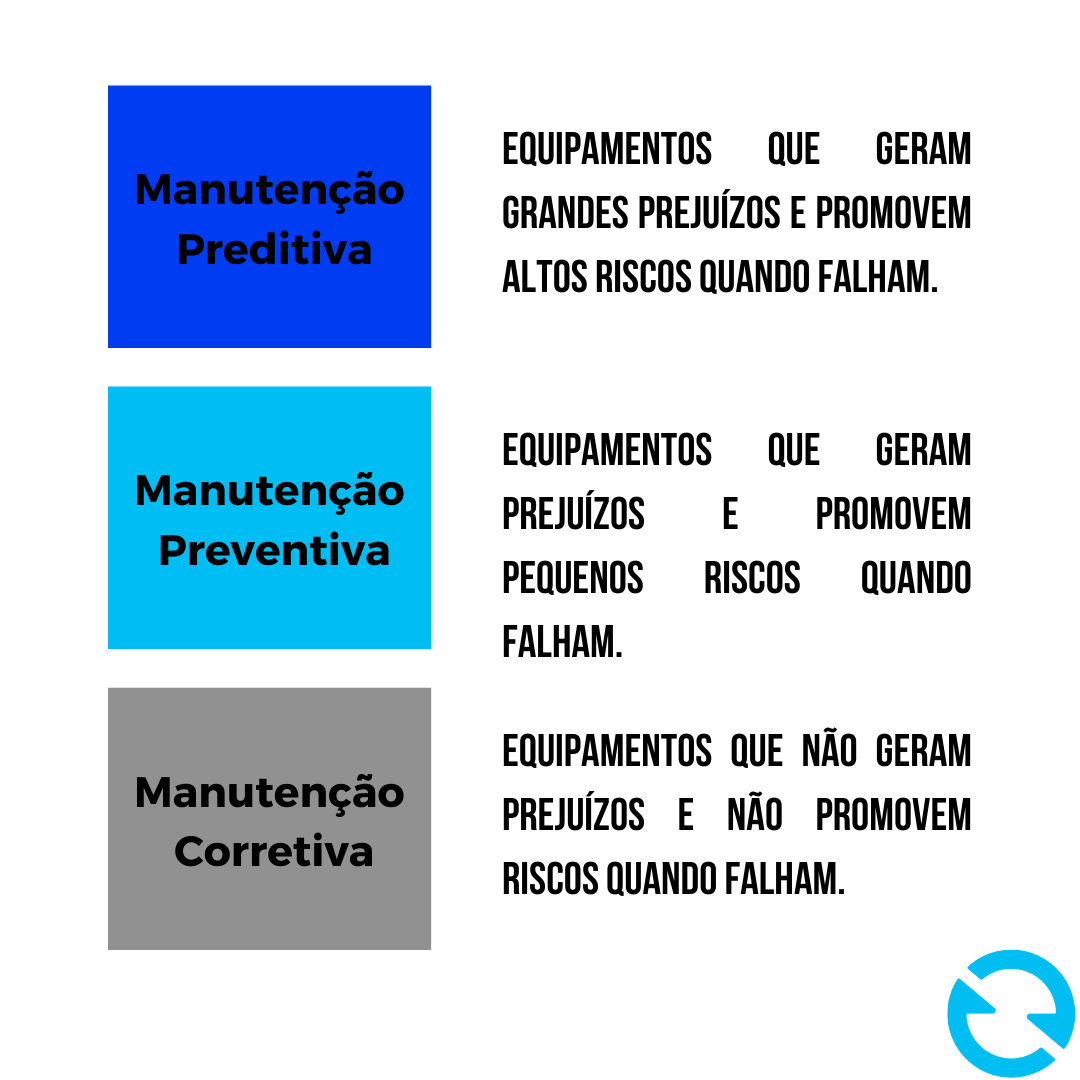
Eficiência operacional é crucial para o desenvolvimento de um negócio. Conheça mais e saiba como melhorar seus processos no nosso conteúdo.
Como fazer um planejamento de manutenção preventiva?
Um bom planejamento da manutenção preventiva é importante para evitar desperdícios de recursos como materiais, mão de obra e tempo. Para fazer um plano de manutenção preventiva na sua empresa, recomenda-se seguir os seguintes passos:
1. Levantamento de informações
Inicialmente é necessário fazer um levantamento de informações acerca de todas as máquinas em funcionamento, como o histórico de intervenções já realizadas. Essa etapa é importante para definir quais equipamentos serão prioridade para a manutenção preventiva, bem como para identificar padrões que definirão a periodicidade das intervenções.
2. Análise dos custos
Nessa etapa é feito o orçamento. Deve-se levar em consideração os custos com materiais necessários, quantidade de colaboradores que irão realizar a manutenção, encargos trabalhistas e uso de softwares para a gestão da manutenção. Além disso, é importante atentar para o custo-benefício da ação, já que optar por comprar peças muito baratas e sem qualidade, por exemplo, pode gerar prejuízos futuramente.
3. Montagem de cronograma
O cronograma é importante para o registro do planejamento realizado. Nele, deve constar a frequência de manutenção, quando ela vai acontecer, quem será o responsável por fazer a intervenção, em quanto tempo a manutenção preventiva deve ocorrer, além dos recursos necessários para tal atividade.
4. Criar check-list de manutenção
Esse check-list servirá para garantir que a manutenção preventiva aconteça corretamente no equipamento. É uma verificação de que a máquina pode voltar à produção com confiabilidade e segurança.
5. Acompanhamento da atividade de manutenção
A gestão da manutenção deve estar atenta ao andamento das atividades de manutenção preventiva. Ademais, conversar com os operadores das máquinas que sofreram manutenção e estruturar KPI’s é indispensável para identificar eventuais oportunidades de melhoria no plano de manutenção.
Além disso, a integração de sistemas de gestão de manutenção e o treinamento contínuo da equipe que trabalha na área são cruciais para o sucesso, principalmente quando lidamos com a Indústria 4.0, que requer a utilização de uma série de softwares e sensores. Esses conceitos são cruciais para a funcionalidade das manutenções e, principalmente, para o sucesso a longo prazo.
Ademais, analisar de forma contínua os resultados complementa o que foi dito anteriormente, pois é possível monitorar se o processo realmente está funcionando da forma que deveria e, caso não esteja, como podemos tomar decisões assertivas para a otimização do processo como um todo.
Logo, esses pontos são essenciais para o negócio, já que várias certificações de qualidade exigem manutenções preventivas, buscando segurança no trabalho e qualidade de produto.
As folhas de verificação podem ser utilizadas como uma ferramenta para garantir que todas as etapas da manutenção preventiva sejam seguidas corretamente, ajudando a identificar problemas antes que eles se tornem falhas graves. Saiba mais no nosso texto.
Ferramentas e softwares para gestão da manutenção preventiva
Com o avanço tecnológico, diversas ferramentas digitais, especialmente os Sistemas Computadorizados de Gestão de Manutenção (CMMS), têm sido desenvolvidas para auxiliar no planejamento e na execução da manutenção preventiva. Veja abaixo algumas dessas soluções, suas funcionalidades e benefícios:
1. Manusis 4.0: o Manusis 4.0 é uma plataforma brasileira que se concentra na manutenção preditiva e preventiva. Ela permite o monitoramento em tempo real dos equipamentos, utilizando dados para prever falhas e programar manutenções antes que ocorram problemas significativos. Essa abordagem proativa ajuda a reduzir custos e aumentar a eficiência operacional.
2. Engeman: o Engeman é um CMMS nacional projetado para a gestão de manutenção em diversos setores. Ele oferece funcionalidades como o gerenciamento de ordens de serviço, controle de estoque de peças e acompanhamento de indicadores de desempenho. Sua interface intuitiva facilita a adoção por equipes de manutenção, contribuindo para a melhoria contínua dos processos.
3. SAP PM: integrado ao sistema ERP da SAP, o módulo de manutenção (SAP PM) é ideal para empresas que já utilizam essa plataforma. Ele proporciona uma gestão abrangente dos processos de manutenção, desde o planejamento até a execução, integrando dados financeiros e operacionais. Essa integração permite uma visão holística dos ativos e dos custos associados.
4. IBM Maximo: o IBM Maximo é uma solução robusta para a gestão de ativos e manutenção industrial. Ela oferece funcionalidades avançadas, como gestão de ordens de trabalho, planejamento de manutenção preventiva, controle de inventário e análise de dados para otimização de processos. Sua escalabilidade e flexibilidade o tornam adequado para organizações de diferentes portes e segmentos.
5. Fracttal: o Fracttal é um software baseado em nuvem que incorpora inteligência artificial para prever falhas e otimizar a manutenção. Ele permite o planejamento de manutenções preventivas, criação digitalizada de ordens de serviço e armazenamento de informações dos ativos na nuvem, acessíveis em tempo real. Essa abordagem facilita a tomada de decisões informadas e a melhoria contínua dos processos de manutenção.
A adoção de um CMMS adequado pode trazer diversos benefícios, incluindo a redução de custos operacionais, aumento da vida útil dos equipamentos, melhoria na eficiência das equipes de manutenção e melhor planejamento estratégico das atividades. É fundamental avaliar as necessidades específicas de cada organização para selecionar a ferramenta que melhor se alinha aos seus objetivos e desafios.
Indicadores de desempenho para manutenção preventiva
Indicadores de desempenho são essenciais para monitorar e aprimorar a eficácia da manutenção preventiva. Dois dos principais indicadores são o MTBF (Mean Time Between Failures) e o MTTR (Mean Time To Repair).
MTBF (Tempo Médio Entre Falhas): O MTBF representa o tempo médio decorrido entre as falhas de um equipamento. Este indicador calcula o intervalo médio em que um equipamento opera sem apresentar falhas. Quanto maior o MTBF, maior a confiabilidade percebida do equipamento.
MTTR (Tempo Médio para Reparo): O MTTR é o tempo médio que a equipe de manutenção leva para reparar um equipamento após uma falha. É calculado dividindo o tempo total necessário para reparo ou manutenção pelo número total de reparos realizados em um período específico. Quanto menor o MTTR, maior a eficiência da equipe de manutenção.
Monitorando esses indicadores, é possível identificar pontos críticos e áreas que necessitam de melhorias, contribuindo para a otimização das estratégias de manutenção e aumentando a eficiência das operações de manutenção.
Exemplos de manutenção preventiva
Segue abaixo alguns exemplos de atividades de manutenção preventiva dos equipamentos:
- Inspeção Sensitiva
A equipe de manutenção realiza a inspeção por meio dos sentidos (tato, olfato, paladar, audição ou visão), buscando identificar uma anormalidade no funcionamento do equipamento. Esse tipo de inspeção não garante a identificação de falhas potenciais.
- Inspeção Instrumentada
Esse tipo de inspeção é feito com o auxílio de instrumentos de fácil manuseio, como o termômetro. O objetivo é a identificação de anormalidades e possíveis falhas. Diferentemente da inspeção sensitiva, a inspeção com instrumentos permite a identificação de falhas potenciais em seu estágio inicial.
- Substituição de itens desgastados, limpeza, ajustes e lubrificações
Essas atividades de manutenção preventiva garantem a reconstituição do estado inicial do equipamento. O objetivo é garantir com que o equipamento continue desempenhando a sua função normalmente.
Tendências e inovações na manutenção preventiva
A Indústria 4.0 trouxe avanços significativos para a manutenção preventiva, integrando tecnologias como Inteligência Artificial (IA), Machine Learning (ML), Internet das Coisas (IoT) e sensores inteligentes. Essas inovações permitem um monitoramento mais preciso e uma gestão proativa dos equipamentos industriais.
A análise preditiva utiliza dados históricos e em tempo real, processados por algoritmos de IA e ML, para prever falhas e otimizar a manutenção. Essas tecnologias identificam padrões e anomalias no desempenho dos equipamentos, permitindo ações corretivas antes que ocorram falhas críticas. Por exemplo, a IA pode prever quando uma máquina está prestes a apresentar problemas, possibilitando a programação de manutenção antes que a falha aconteça.
A Internet das Coisas (IoT) envolve a interconexão de dispositivos físicos com a internet, permitindo a coleta e troca de dados em tempo real. No contexto industrial, sensores inteligentes monitoram continuamente o estado e o desempenho de máquinas e equipamentos. Esses sensores capturam dados como temperatura, vibração e umidade, que são analisados para identificar possíveis problemas antes que se tornem críticos. Por exemplo, sensores IoT podem detectar variações de temperatura em um motor, indicando superaquecimento iminente, permitindo a intervenção antes que ocorra uma falha.
A integração de IA, ML, IoT e sensores inteligentes na manutenção preventiva resulta em estratégias proativas baseadas em dados, melhorando a eficiência operacional, minimizando o tempo de inatividade e otimizando os processos de produção. Essas tecnologias permitem que as empresas antecipem problemas, planejem manutenções de forma mais eficaz e aumentem a confiabilidade de seus sistemas e equipamentos.
Saiba como maximizar os ganhos e diminuir as perdas no processo produtivo da sua empresa! Acesse nosso ebook gratuito sobre arranjo físico.